Funded project- Reducing 50% of construction waste through prefabrication
The project will validate the waste, cost and time saving potential of prefabrication in a Victorian context, providing both the evidence-base and business case to support future private investment in the sector.
Background
Cross Laminated Offsite Solutions (CLOS) is an established Off-Site Manufacturing (OSM) provider offering engineered timber components and systems to the Victorian property market. Utilising Cross Laminated Timber (CLT) and glulam, CLOS delivers structural rigidity, low embodied carbon, and precise mechanised production.
CLOS specialises in constructing volumetric and flat pack elements at its factory in Geelong, Victoria. Founder and CEO John Fitzgibbon has expertise in traditional and offsite construction which drives CLOS's mission to address construction inefficiencies and to improve building practices.
The problem
The construction industry faces challenges related to cost, supply chain coordination, and environmental impact. In Australia, construction contributes to a significant portion of greenhouse gas emissions and generates a substantial amount of waste. Industrialised construction, particularly through Off-Site Manufacturing (OSM) or prefabrication, offers solutions to reduce waste, improve material flows, and enhance quality and efficiency. However, commercial advancement of OSM in Australia has been limited.
The project
The project focuses on demonstrating waste avoidance, cost reductions and increased performance of prefabricated homes. It will assess against traditional construction methods and showcase best practice with the assistance of the collaborative partners. The project aims to build 28 prefabricated townhouses in Geelong. A Material Flow Analysis (MFA) will be undertaken to collect data, benchmark and improve the waste reduction opportunities against standard Victorian building practice.
A business case will be developed to share learnings with industry to support future investment in prefabrication in Victoria. The project will focus on supply chain integration to operationalise waste reduction in the local timber supply chain while demonstrating a state-of-the-art tooling upgrade.
CLOS presents advantages of enclosed and monitored production for improved project outcomes. The controlled environment of off-site manufacturing enhances quality, precision, and worker experience, providing safety factors and overcoming weather challenges.
Project progress
Key deliverables | Status |
---|---|
Source and install equipment, including overhead gantry system, cut off saws, handling equipment and joist press. Source materials, commence design for pre-fabrication, package and prepare for site delivery. Conduct strategic assessment to identify barriers and opportunities and conduct stakeholder workshops. | Complete |
Undertake primary on-site data collection, sort, and analysis data. Develop detailed designs for manufacture using CLOS technology. Test design on affordable housing site in Melbourne. Determine cost design for prefab construction. | Complete |
Develop a detailed business case. Conduct additional stakeholder workshops. Timber supply chain integration: verify data, analyse opportunities and implement system. Undertake material flow analysis (phase one): review relevant literature and standards. Define systems and process balancing. | Complete |
Install 28 townhouses in Geelong. Collect data and conduct quality assessments. Material flow analysis (phase 2): outline modelling for material flow. Analyse and report on findings. Identify opportunities for further reduction. | In progress |
Prepare a case study to be shared with the public. |
Challenges
In 2022 there were major challenges in sourcing materials, including Laminated Veneer Lumber (LVL) and Machine Graded Pine (MGP). These external factors influencing supply and demand in the market highlghts the difficulties in procuring construction materials. To address shortages, alternate suppliers and trucking services were sourced. A recently procured Computerised Numerical Control (CNC) machine has assisted with the challenges in productivity due to labour shortages. To resolve some of these issues, additional team members joined to optimise data tracking, waste material handling, and assist with changes to designs and drawings.
Insights
The project will provide an opportunity for the industry to transition towards circularity and apply modern construction methods, including the implementation of robust data tracking systems for delivery, manufacturing, and waste management prior to fabrication.
It’s important to establish a reliable material supply chain by directly engaging with manufacturers and reducing reliance on subcontractors and expanding in-house labour capabilities. Industry needs to consider streamlining manufacturing, material handling, and waste management processes.
From the grantee
The CEBIC funding has been instrumental in CLOS optimising their offsite prefabricated system through obtaining true data on a real project. The traditional construction method of delivering raw materials to site followed by tradespeople “building” onsite is tired and vulnerable to today’s challenges. In this current climate, there aren’t enough skilled trades, material costs are inflated and there are too many site delays.
“Our company's default approach is to question is “what’s the best material to use. When designing buildings, CLOS and its design team considers how these buildings can be “added to or deconstructed” after their initial use is ready for change.
"A key focus of CLOS is to ensure we’re providing better solutions to construction practices. We use sustainable materials that are responsibly sourced. We use advanced manufacturing techniques to be more effective in fabricating components to assemble our buildings. We have invested in ensuring the right materials are used in the right applications."
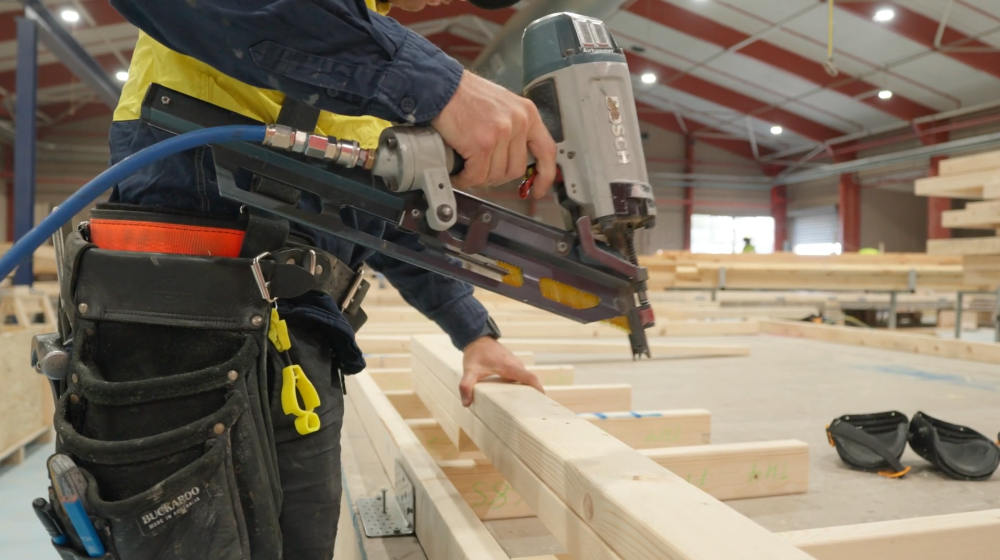