Funded Project – Biofibres for sustainable apparel inspired by Humble Bee
Develop and research a bio-inspired textile as a viable polyester alternative. The new fibres and textiles will be made from recombinant protein-based biopolymers based on the nesting material of a native Australian solitary bee.
Background
Deakin University is renowned for its exceptional teaching and research, with a strong emphasis on industry collaboration. The Institute of Frontier Materials, located within Deakin, is a world-leading research institute dedicated to redesigning functional materials for a circular economy in partnership with commercial entities worldwide. The institute's primary focus lies in the field of fibres and textiles research, as evidenced by its involvement in the ARC Research Hub for Sustainable and Functional Fibres. This collaborative initiative, comprising 11 industry partners, aims to translate cutting-edge research into circular products and technologies.
In this project, Deakin University joined forces with Humble Bee Bio to characterise a bee-inspired biopolymer suitable for the sustainable production of a bio-yarn. The goal was to explore industrial scale spinning techniques to enable the mass manufacturing of this eco-friendly yarn. This project aimed to close the loop in apparel manufacture by replacing non-renewable synthetic yarns, with circular textiles made from bee-inspired biopolymer yarns.
The problem
In Australia, the significant impacts of the apparel industry include climate change, microplastic pollution from laundering, and end-of-life disposal, considering the country's position as the second-largest consumer of apparel.
Apparel waste is a rapidly growing global problem, with an estimated 400 million tonnes generated annually. Unfortunately, there are currently no large-scale recycling options available, leading to the widespread disposal of these items. Compounding the issue is the prevalent use of materials derived from non-renewable and non-degradable petrochemicals.
The project
This project aimed to develop a novel, circular bioinspired textiles. The fibres and textiles were made from recombinant protein-based biopolymers derived from the nesting material of a native Australian solitary bee. Partnering with Humble Bee Bio (HBB), Deakin used sustainable and energy-efficient bioreactors to produce the biopolymer through fermentation, building upon previous research.
The bio-textiles underwent thorough evaluation by HBB's apparel designer and third-party manufacturers and designers to assess their viability. Feedback from the evaluations guided further development of the biopolymer production process and product manufacturing.
Deakin University characterised the biopolymer and established scalable spinning technology to produce bio-yarns. These yarns were used to create textile samples for demonstration.
Objectives
Create two new circular products
Two circular products, yarn and apparel textile, will be created using the bee biopolymer. Yarn production minimises waste by using biopolymer, water, and solubilising solvent. Recovering and reusing the solvent and water align with industry standards. Excess biopolymer waste can be used as feedstock for 2nd generation biopolymer.
Technological innovation
This project represents technological innovation in Victoria and across Australia. The utilisation of recombinant genetics and bioreactors to produce protein-based polymers from bee-inspired sources is unprecedented. Only HBB has employed this method, making them the sole company globally with such capabilities. The supply of biopolymer through Victorian infrastructure, facilitated by CSIRO, further highlights the project's uniqueness.
Project progress
Key deliverables | Status |
---|---|
Biopolymer characterisation, supply, purification, and characterisation by Humble Bee Bio. Undertake characterisation of biopolymer in context of suitability for wet spinning. | Complete |
Developing prototype films and/or coatings from Humble Bee Bio biopolymer formulations. Undertake development work on non-fibrous materials. Characterise chemical and physical properties to inform fibre production and other potential applications. | Complete |
Production of fibrous materials incorporating Humble Bee Bio biopolymer. Manufacture fibrous materials containing biopolymer. Characterise the materials developed, including standard characterisation, and performance. | Complete |
Production and comparative evaluation of textiles developed for targeted applications. | Complete |
Undertake project evaluation and business case/economic analysis for final report. | Complete |
Challenges
Material Supply and lead times: there was a high amount of material required for the research and lead time to get material led to delays. This was mitigated by careful experimental design and prioritisation of experimental workflow to ensure best outcomes for the project and industry partner.
Outcomes
- The project created two types of yarn and one textile from an innovative sustainable biomaterial developed by Humble Bee Bio.
- A deepened understanding of the material, paving the way for future research and development.
- In terms of contribution to the circular economy, the project sparked additional research into these novel biomaterials in two significant fields.
- The potential as sustainable cosmetic additives were explored.
- The application in the biomedical sector was investigated, particularly focusing on their biocompatibility and their utility as scaffolding materials in medical implants, in collaboration with the Deakin School of Medicine. This expansion into new research areas underscores the project's role in promoting sustainability across various industries.
Insights
- When considering the launch of a circular economy project, Victorian businesses or organisations should set ambitious goals and embrace a forward-thinking, visionary approach. It's essential to balance this ambition with a willingness to take calculated risks, while also maintaining realistic expectations regarding what can be achieved. This balance is crucial given the constraints often encountered, such as strict project timelines, limited funding, and the current state of scientific knowledge and technology.
- Embarking on such research is not just about innovation for its own sake; it's a vital step towards a more sustainable and environmentally friendly business model. The transition towards a circular economy requires a shift in mindset from linear 'take-make-dispose' processes to more regenerative and sustainable practices. This involves designing products and systems with reuse, recycling, and resource recovery in mind from the outset.
- Engaging in circular economy projects can position businesses as leaders in sustainability, potentially opening new markets and customer segments. It can also lead to cost savings in the long term through more efficient use of resources and reduced waste.
- It's important for businesses to conduct thorough planning and research before diving into such projects. This includes understanding the specific needs and opportunities within their industry, potential environmental impacts, and the regulatory landscape.
- Collaboration with other businesses, research institutions, and government bodies can also provide valuable insights and support.
- While the journey towards a circular economy presents challenges, it also offers significant opportunities for innovation, growth, and sustainability. By aiming high, embracing risk with caution, and staying informed and adaptable, Victorian businesses can make meaningful contributions to a more sustainable future.
What’s next?
Further research and investment into these materials and products is currently being undertaken within the Deakin and HBB collaboration. This project has also led to the expansion of current projects to investigate additional biomaterials that were developed after the start of this project.
From the grantee
“As a materials scientist, the importance of funding from initiatives like the Circular Economy Business Innovation Centre (CEBIC) is pivotal in advancing our journey towards circularity. This funding has been a game-changer, enabling us to fast-track our research into sustainable materials, foster industry collaborations, and transition from theoretical research to market-ready solutions. Our organisation prioritizes sustainability and circularity to address the environmental challenges posed by the traditional 'take-make-dispose' model, meet growing consumer demand for sustainable products, and fulfill our responsibility towards environmental stewardship.”
– Dr Dylan Hegh Manager Research Initiatives Deakin University
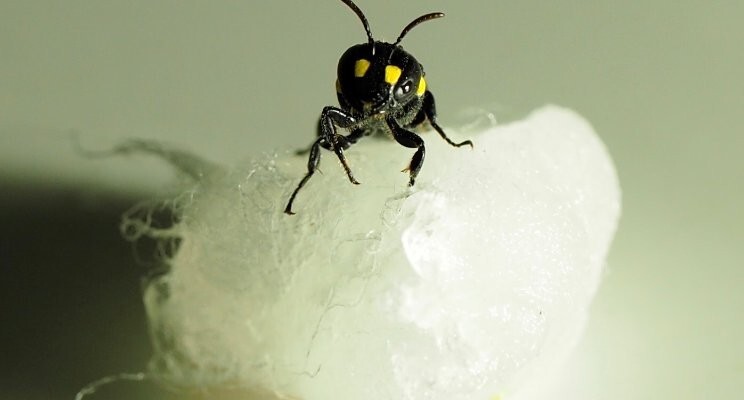