Funded project – Melbourne's first zero waste food upcycling hub
A Victorian-first food processing hub in the South Werribee growing district that upcycles surplus vegetables and by-products into value-added foods and ingredients. They are also helping local growers use 100% of their crop while minimising food waste on farms, in pack-houses, and during food manufacturing.
Background
Nutri V turns surplus vegetables that would otherwise go to waste on farms into vegetable powders and snacks, giving food waste a second life and farmers an additional revenue stream. Its aim is to improve Australians’ health, reduce food waste, and care for the environment by using sustainable farming practices.
The facility the company built with funding help from CEBIC, is the first of its kind in Victoria. It has the capacity to transform almost 8,000 tonnes of surplus vegetables and vegetable offcuts every year into new food products. The facility also has the potential to provide over 60 million additional serves of vegetables, recovered from waste, for business-to-business and business-to-consumer sales and is projected to create 11 new jobs.
The company is a collaboration between Fresh Select, a leading fresh-produce supplier with over 60 years of Australian farming history, and Australia’s national science agency, Commonwealth Scientific and Industrial Research Organisation (CSIRO).
Nutri V offers a whole-of-vegetable solution to improve health and reduce unnecessary plant-food waste to maximise our planet’s resources. Fresh Select is one of the largest producers of lettuce and vegetables like broccoli and cabbage in Australia, with operations across the country.
The plan is to scale up this technology and expand it to other vegetable producers across Australia.
Objectives
The objectives of the project were to:
- Reduce the generation and disposal of vegetable waste at the primary production and processing (pack-house) supply chain stages, and to extend this benefit to other agricultural businesses in the Werribee South growing district.
- Establish a new processing plant with the capacity to accept and transform 7,900 tonnes of low-grade vegetables, surplus vegetables, and vegetable offcuts into new food products and ingredients each year.
- Create a new circular economy business model and a new circular economy service for growers in the Werribee South agricultural district as an alternative to other waste disposal or recycling processes.
- Create new sustainable products for sale to businesses and consumers based on the circular economy principles of eliminating waste and pollution and keeping products and materials in use for longer.
- Support the development and adoption of zero-waste farming in Victoria and ultimately achieve 100% agricultural production yield on farms in the Werribee South growing district.
- Create new long-term circular-economy-based jobs.
The project has been split into stages to allow for proof of concept, scaling commercialisation, and then operation at full capacity.
Process
The grantee used the funding provided by Sustainability Victoria to purchase, install, and commission part of the processing plant, specifically a drying unit to process vegetables into nutrient powders – a shelf-stable product for a longer shelf life.
Once the equipment arrived on site, Nutri V did some testing to ensure smooth production.
The facility can transform almost 8,000 tonnes of surplus vegetables and vegetable offcuts every year into new food products, creating 11 new jobs. Nutri V will commercialise these products. The project also included market engagement, prototype creation, testing, and quality assurance compliance to make sure products can be sold.
Challenges
- There has been a 27% overspend due to higher than anticipated equipment ventilation costs, and concrete and steel price increases.
- There was a 38% overspend for the packing equipment because the project required a more expensive machine than the one that was trialled.
- COVID-19 lock downs and state border closures slowed the project down slightly, resulting in more internal trials without the dryer manufacturer.
Ventilation
- Ventilation was an issue, which Nutri V will approach differently in the future. Ideally ventilation should be approached as a separate project.
Consumer acceptance
- Consumer acceptance was another hurdle to success and wider application use from food manufacturers. Shifting the culture from cheap imported ingredients to quality Australian ingredients remains an ongoing barrier.
- The general view that recovered food or food waste of no value is an ongoing education piece.
Insights
Put effort where it makes the most difference
- Pre-commercialisation work demonstrated viability and value, and this process enabled Nutri V to mitigate project risks.
- Consulting with equipment experts, quality assurance and a ventilation specialist before any work commences will ensure all information on the project requirements are clear before commencement.
- The project required many trials and tests to be able to successfully operate the equipment and production line using 5 different vegetable feedstocks.
- Through testing, Nutri V was able to learn about the best applications for various vegetables, backed by strong data.
Outcomes and impact
- The facility is now fully operational. Nutri V has increased processing capacity to 7,900 tonnes. There are now 3 products on the market, with 8 more in prototyping stage. Nutri V also created several new product lines to be used in other products.
- New product lines are currently undergoing testing and are in the research, and development (R&D) phase. Along with taking excess product and seconds from other farms, Nutri V is offering R&D and toll drying services to other producers to address their waste, where they have end products in mind. There are 3 snack products now in the market from this project.
- The Nutri V process has successfully extended the life of vegetables from 14 days to 365 days, with a goal of providing a shelf life of up to 2 years.
- Businesses are excited about the Nutri V process and have expressed interest in being involved and using the product.
What’s next?
- Nutri V has created a circular solution to food waste and will continue to build awareness of its innovation and work with food companies and consumers on long- and short-term options to increase exposure.
- Nutri V has a 2-year plan to expand its current feedstock lines, with a goal to be incorporated into 15 other end products: 6 of its own and 9 from external companies.
- There is a dedicated salesperson to drive sales and manage customer engagement. Nutri V will continue to promote and attend events to drive awareness of its products, services and solutions.
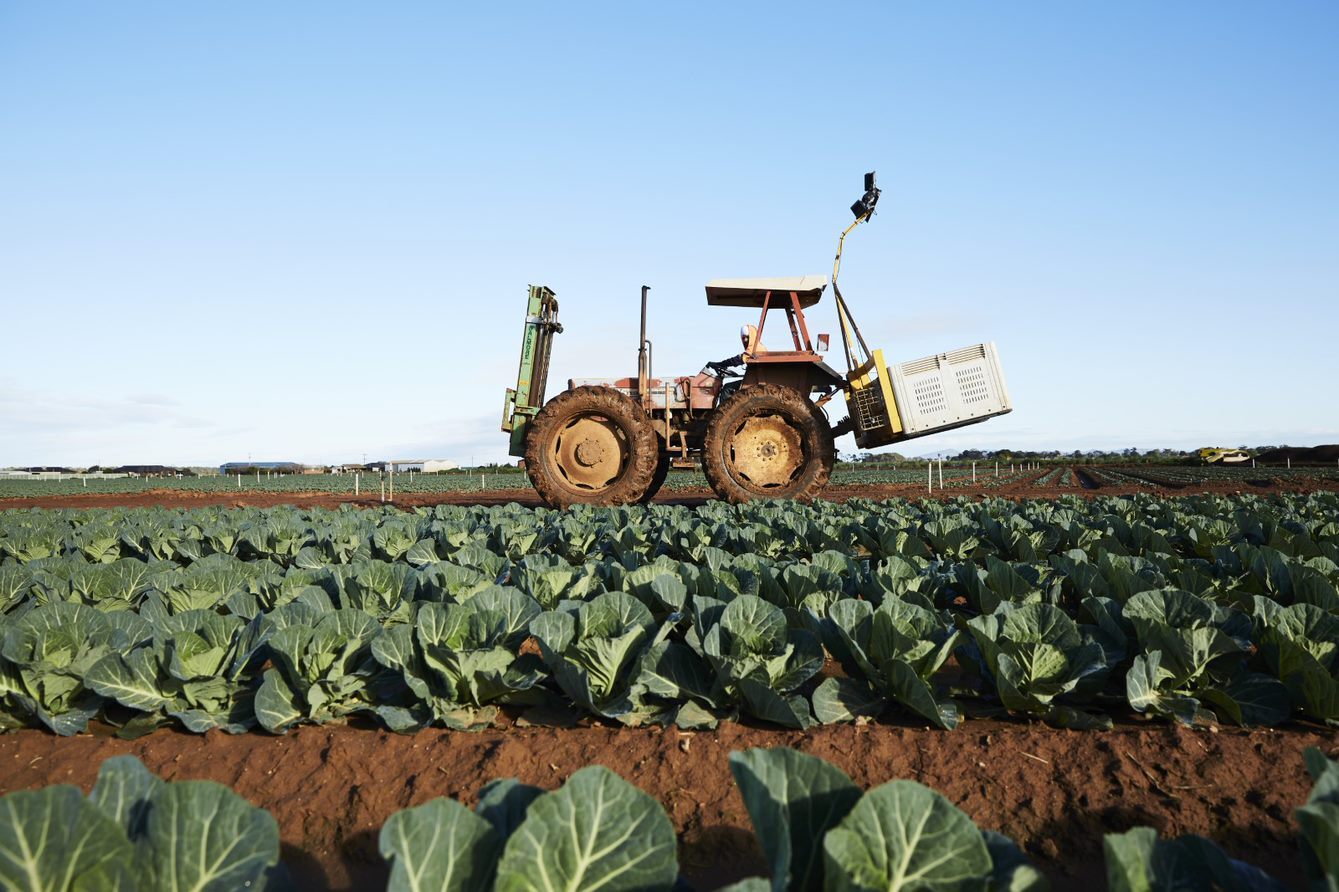
More information
Visit Nutri V and watch the Fresh Select video about turning surplus vegetables into nutritional powders and cutting food waste.