Funded project – Formwork for a sustainable future
This project developed and piloted a prototype for a new, reusable ‘Modular Interconnecting Formwork System’ (MIFS) to demonstrate a sustainable alternative to existing single-use formwork used across the construction industry.
Background
Mortar Art, a prototyping and small batch manufacturing service based in Melbourne, embarked on the journey to pilot the 'Modular Interconnecting Formwork System' (MIFS) project. The aim of the project was to revolutionise construction practices by introducing a novel approach to formwork, utilising poured mediums such as concrete and rammed earth.
The project team consists of experts from diverse backgrounds, including building design, construction, and manufacturing. Extensive research helped to determine the best approach to address Victoria's plastic waste recycling crisis. During this process, the team identified an opportunity to develop a formwork system that could easily be implemented in the construction sector.
The team involved recognised the potential to manufacture the system in a manner that is resilient to waste contamination, addressing a major hurdle in plastic recycling.
Objectives
The project aimed to achieve the following objectives:
- Design and develop a new reusable formwork system as a sustainable alternative to existing single-use timber formwork.
- Demonstrate the effectiveness of this system by constructing a pilot building using the reusable modular formwork.
- Raise awareness and educate the industry about the opportunities presented by this innovative approach, including providing intellectual property (IP) through an open-source platform that can be utilised by relevant businesses.
- Demonstrate the feasibility of producing plastic tooling at a low cost and distributing it to the locations where plastic waste is generated, to streamline the logistics involved in current recycling processes.
Process
Mortar Art undertook several crucial steps in the development of the formwork system project. Firstly, they successfully established a prototype compression moulding tool capable of producing bricks from recycled plastic. These bricks served as the central component of the proposed formwork system.
To showcase the effectiveness and viability of the formwork system, Mortar Art constructed a demonstration structure in Benambra, a regional area in Victoria. The structure serves as a tangible example of the system's capabilities and functionality.
During the latter phase of the project, the team created a comprehensive range of visual assets, including scale models, detailed 3D renders, high-quality photographs, and captivating videos. These materials played a pivotal role in effectively conveying the multitude of benefits and exceptional features offered by the formwork system to stakeholders and industry professionals.
To facilitate knowledge sharing and encourage replication of the project, the team created a comprehensive documentation of the methods and processes involved in the project's implementation. Technical specifications and instructions were available under an open-source intellectual property license on Recyclopaedia and other platforms. It enables interested parties to access and utilise the information for their own projects, contributing to the wider adoption of circularity and sustainable practices.
Challenges
Starting a project during an ongoing pandemic presented challenges, resulting in the project taking longer than originally anticipated. An example of the challenges faced occurred on the day when the team was scheduled to commence the site works for the final milestone. Unfortunately, a key participant tested positive for COVID-19 and had to isolate, leading further delay in the project's progress.
Delays in the availability of certain machine tools necessitated careful planning to mitigate procurement delays. While designing and machining moulds internally provided valuable insights into the production processes. It was not necessarily more efficient than outsourcing manufacturing while retaining in-house design capabilities.
Insights
An important insight from the project is the ease of using the formwork system. Contrary to expectations, one worker can construct walls efficiently and intuitively, which practically streamlines construction and enhances productivity.
Reducing reliance on key personnel was another valuable lesson. Shifting the project lead to a managerial role enabled distributed decision-making and ensured smooth progress, even without specific individuals.
The team identified wasted feedstock materials, specifically plastic lids from milk bottles. Through the prototype project, they demonstrated using these waste materials as substitutes for products made from virgin timber and plastic. Such innovative approach can be replicated for other items, promoting circularity, and reducing reliance on new materials.
Outcomes
Practical application
Design revisions improvements ensured ease of installation, which is highly encouraging for potential commercial applications, as traditional formwork techniques often demand a high level of skill from installers. Minimal additional training will be required for MIFS, which not only streamlines the adoption process but also enhances the potential for widespread implementation and successful use of the innovative formwork system.
Waste avoidance
The MIF system has the potential to prevent over one tonne of waste per standard house build by utilizing reusable, repairable, and recyclable formwork. To this effect, it results in a reduction of raw materials, such as polystyrene foam, formply, and other timber products.
Components of the formwork were manufactured using plastic sourced from drink bottle lids. This product is not typically recycled well. There is potential to source alternative materials for MIFs such as plastics recovered from e-waste processing, used car parts, off-cuts from industrial plastic waste, bulk packaging materials, and compacted polystyrene foam.
Successful demonstration
Building a permanent wall on the demonstration site effectively depicts the formwork system. There are plans to expand demonstrations by building a small hut, and initial pilot use within the commercial construction industry. Commercialisation should be achievable with basic investment in tooling for larger scale manufacture of the tooling.
What’s next?
MIFS will undergo pilot testing in various commercial and research and development construction projects to gather comprehensive documentation on its optimal utilisation. Additional formworking tools will be manufactured and demonstrated during these pilots, contributing to the public domain intellectual property, and increasing the product's appeal to architects and builders.
A formulated business case will seek potential funding for the development of an automated tool, similar in size to a vending machine. The tool will enable the production of MIFS at industrial sites where plastic waste is generated, providing an immediate avenue for commercialization of the product.
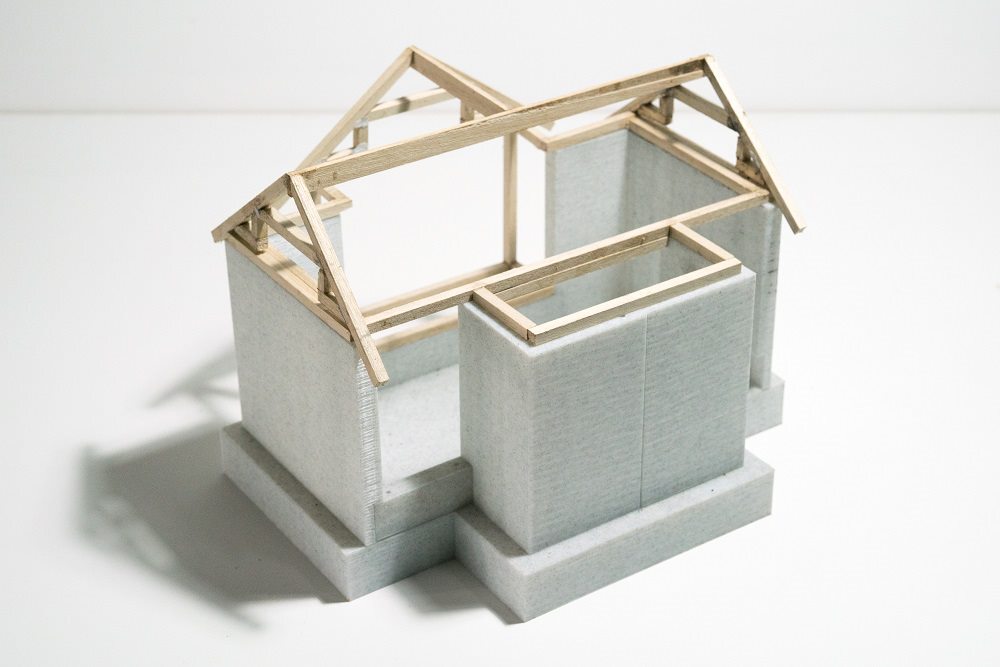